Exemplifying FIBC Excellence in a
Controlled Environment
Our Clean Room Facility Defines Professional Packaging Standards.
Clean Room Bags -
- One-Way Transportation
- Easy to Dispose
- Cost Effective
- Minimum Handling
- Less Space Requirement of Handling Empty and Filled Bags
However the main problem expected in this mode of packaging is cleanliness of the bag hygiene condition, contamination and protection of the content properties such as aroma, colour etc.
To over come this problems the FIBC industries have developed clean room bags to accommodate all food and pharma packaging needs and around the world this clean big bags (FIBC)are used by all food and pharma industries successfully.
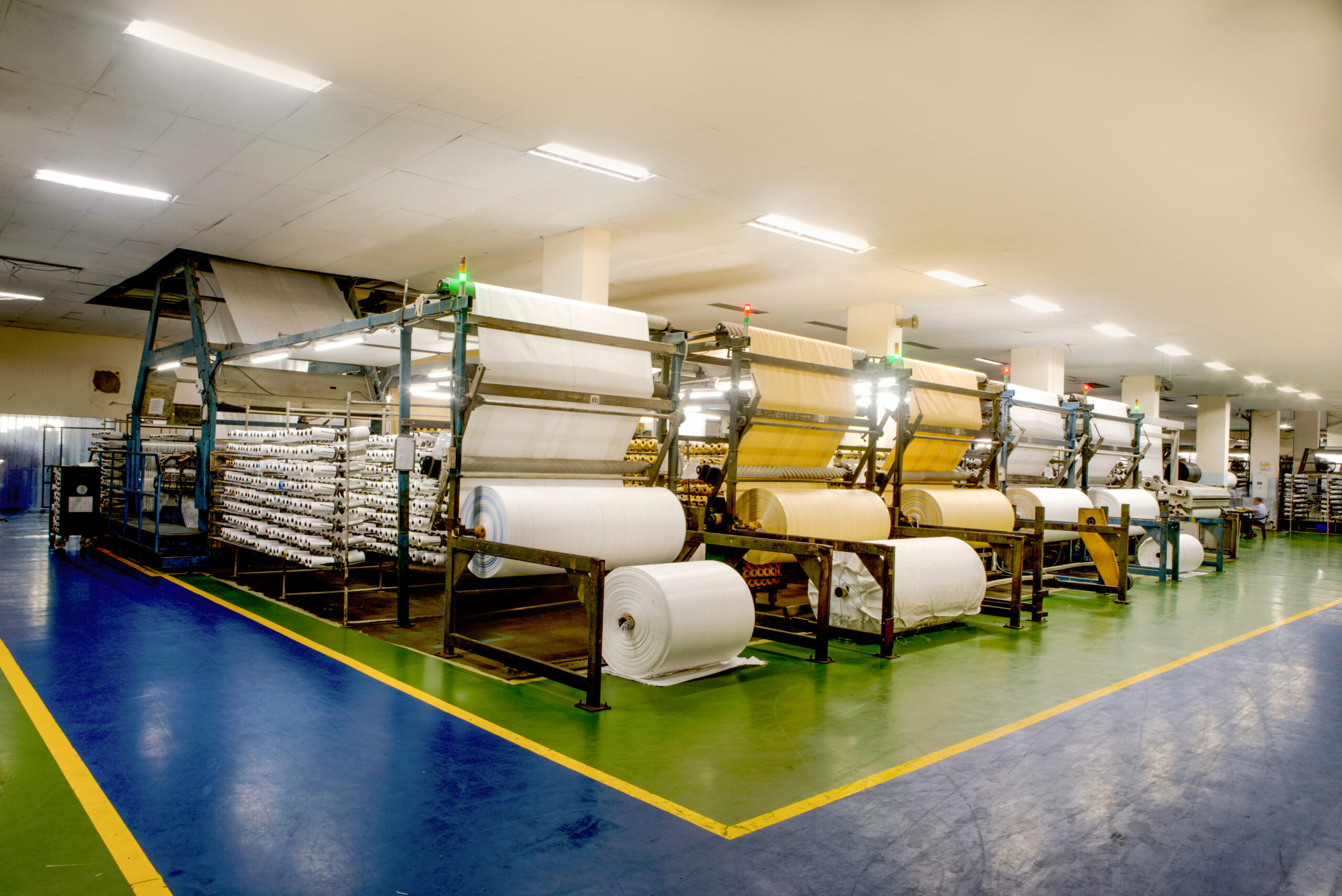
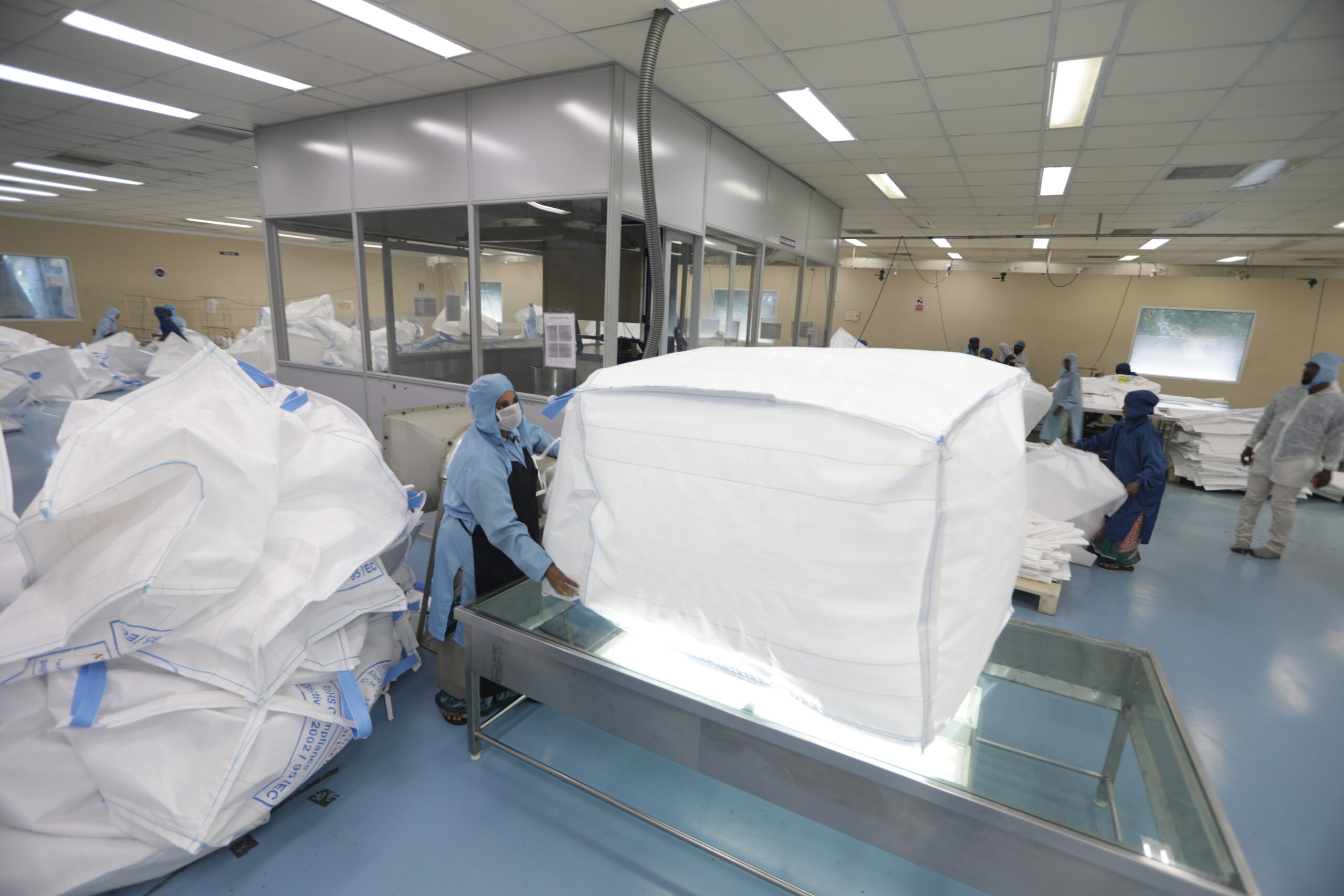
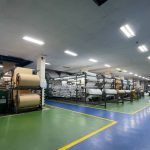

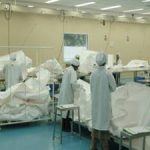
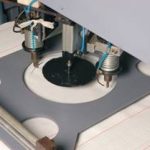
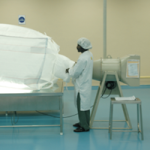
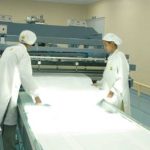
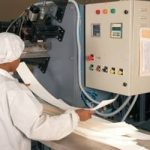
Clean Room Facilities
Jumbo Bag produces food and pharmacy application FIBCs from its state-of-the art Clean Room facility to fulfill stringent customer requirements. The facility is well integrated from fabric stage to packing and is fully air conditioned with controlled atmosphere. The complete plant is maintained at most hygienic conditions to adhere to universal standards such as AIB, BRCGS, ISO 22000, etc.
All the raw materials and lubricants are approved for direct food contact to meet food and pharma requirements. The Clean Room is equipped with world-class equipment such as ultrasonic cutting, slitting, and punching to achieve cleaner cut edges without any plastic burns. All sewing machines are fitted with auto thread cutting (cold and heat) to avoid loose threads. Bag cleaning machines are used to clean the bag by high velocity cleaned air.
Before any material enters the clean room, it enters the air lock room, a buffer zone between the clean room and the out side atmosphere. This keeps the clean room pressurized and free from filtrating dirt.
Metal Detectors
Jumbo Bag implemented HACCP (Hazard Analysis Critical Control Point ) in clean room facility to ensure optimum food safety. This facility has been awarded ISO 22000 for food safety management system and BRCGS for packaging.
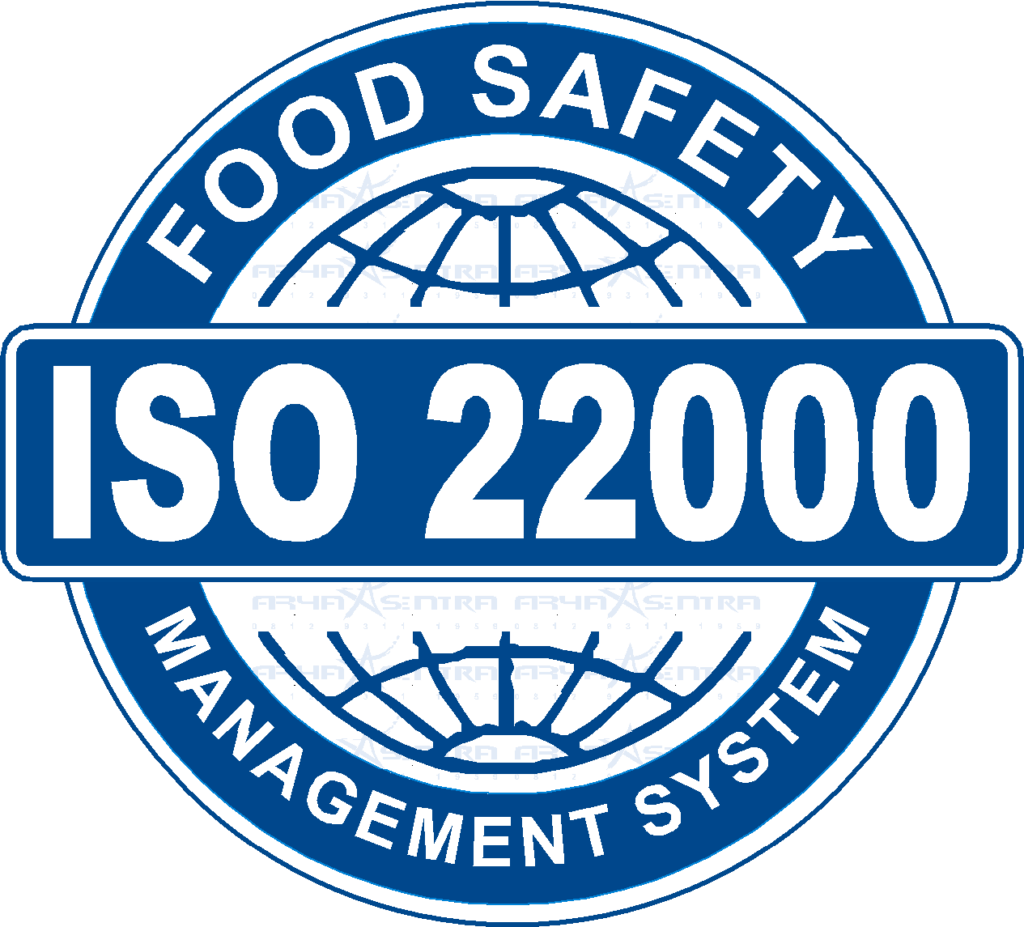
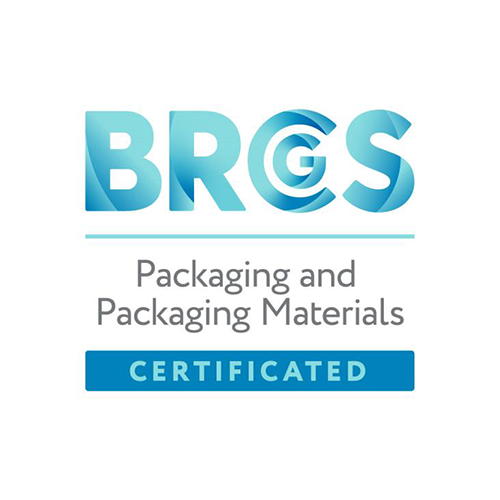